Correct use of automatic pipe cutter blades
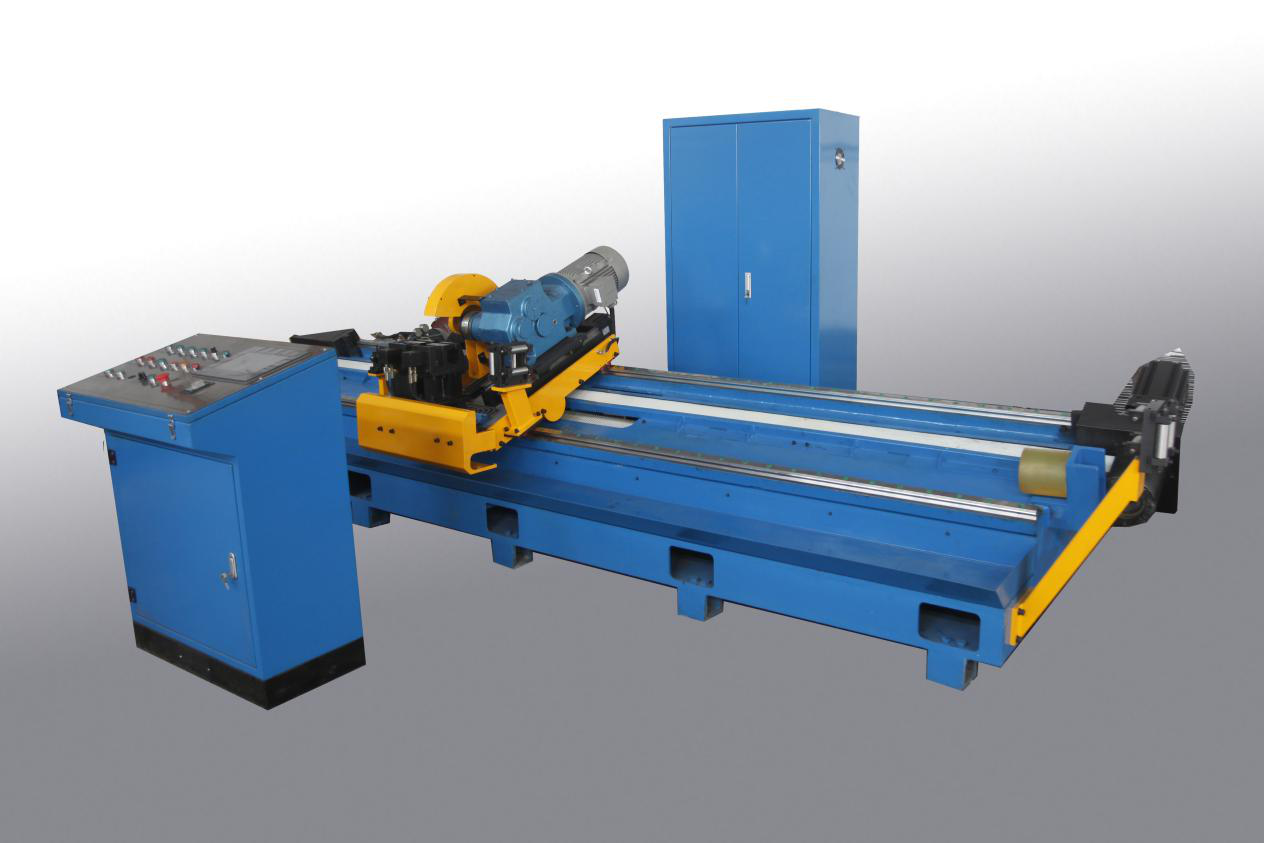
Correct use of automatic pipe cutter blades
(1) Basic requirements for automatic pipe cutting machine saw blades
1. Select the appropriate saw blade according to the design requirements of the equipment. 2. The equipment should be equipped with safety protection devices, such as: protective cover, power-off brake, overload protection, etc. 3. Have professional operators to install and use, wear labored clothing, wear protective glasses, earmuffs, etc. 4. Operators should not wear gloves, long hair should be placed in the work cap, and tie and cuffs should be noted to prevent danger. 5. Keep away from fire and humid environments.
(2) Installation requirements:
1. The equipment is in good condition, the main shaft has no deformation, no trailing jump, the installation is fixed firmly, no vibration, etc. 2. Check the saw blade for damage, whether the tooth profile is complete, whether the saw blade is smooth and clean, and whether there are other abnormalities to ensure safe use. 3. When assembling, make sure that the arrow direction of the saw blade is consistent with the direction of rotation of the device spindle. 4. When installing the saw blade, keep the shaft center, the chuck and the flange clean. The inner diameter of the flange is the same as the inner diameter of the saw blade. Make sure that the flange is tightly combined with the saw blade, install the positioning pin and tighten the nut. The size of the flange should be appropriate and the outer diameter should be no less than 1/3 of the diameter of the saw blade. 5. Before the equipment is started, ensure the safety. If there is a single person operating equipment, jog and idling, check whether the equipment is turning correctly, whether there is vibration, the saw blade is idling for a few minutes, no slip, swing or beat normally. jobs.
(3) Requirements for use:
1. When working, the workpiece should be fixed, the profile positioning should conform to the direction of the knife, so as to avoid abnormal cutting. Do not apply side pressure or curve cutting. The feed should be smooth and avoid the impact of the blade touching the workpiece, resulting in damage to the saw blade, or The workpiece flew out and an accident occurred. 2. When working, if the sound and vibration are abnormal, the cutting surface is rough, or the odor is generated, the operation must be terminated immediately, and the fault should be checked in time to eliminate the accident to avoid accidents. 3. When the pipe cutting machine starts cutting and stops cutting, do not feed the knife too fast to avoid broken teeth and damage. 4. If cutting aluminum alloy or other metal, use a special cooling lubricant to prevent the saw blade from overheating, causing paste, and other damage, which affects the cutting quality. 5. The equipment flute and slag suction device ensure smooth flow to prevent slag from forming into blocks, which affects production and safety. 6. When dry cutting, please do not cut continuously for a long time, so as not to affect the service life and cutting effect of the saw blade; wet film cutting should be cut with water to prevent leakage.
(4) Saw blade maintenance:
1. If the saw blade is not used immediately, it should be laid flat or suspended by the inner hole. The other pieces or feet should not be stacked on the flat saw blade, and the moisture should be protected against rust to avoid the cutting process. The burr, on the deburring machine, will not be able to clean the burr because the burr is too large. 2. When the saw blade is no longer sharp and the cutting surface is rough, it must be repaired in time. Grinding can not change the original angle 3. The inner diameter correction of the saw blade, the positioning hole processing, etc. must be carried out by the factory. If the processing is poor, it will affect the product use effect, and may be dangerous. In principle, the reaming should not exceed the original aperture of 20mm, so as not to affect the balance of stress. 4. The choice of alloy grinding wheel. 1) The resin bond diamond grinding wheel has weak bonding strength, so the self-sharpening property during grinding can be good, it is not easy to block, the grinding efficiency is high, the grinding force is low, the grinding temperature is low, and the disadvantage is that the wear resistance is poor and the wearer wears out. Large, not suitable for heavy duty grinding. 2) Ceramic bond diamond grinding wheel has better wear resistance and bonding ability than resin binder. It has sharp cutting, high grinding efficiency, no heat and clogging, less thermal expansion, easy control precision, and has a rough grinding surface and high cost. . 3) Metal bond diamond grinding wheel has high bonding strength, good wear resistance, low wear, long service life, low grinding cost and high load, but poor sharpness and easy blockage. 4) Abrasive grain size has a certain influence on the clogging and cutting amount of the grinding wheel. Compared with the fine sand grain, the coarse sanding grain has a larger wear depth of the cutting edge, and the grinding wheel is easy to block. 5) The hardness of the grinding wheel has a great influence on the blockage. The high hardness of the grinding wheel is high, which is not conducive to surface heat dissipation, but it is beneficial to improve the processing precision and durability. 6) Grinding wheel concentration selection is an important characteristic, which has a great influence on grinding efficiency and processing cost.
The efficiency is loud, on the contrary, the abrasive particles are easy to fall off, but the optimal binder concentration range is also optimal.
(1) Basic requirements for automatic pipe cutting machine saw blades
1. Select the appropriate saw blade according to the design requirements of the equipment. 2. The equipment should be equipped with safety protection devices, such as: protective cover, power-off brake, overload protection, etc. 3. Have professional operators to install and use, wear labored clothing, wear protective glasses, earmuffs, etc. 4. Operators should not wear gloves, long hair should be placed in the work cap, and tie and cuffs should be noted to prevent danger. 5. Keep away from fire and humid environments.
(2) Installation requirements:
1. The equipment is in good condition, the main shaft has no deformation, no trailing jump, the installation is fixed firmly, no vibration, etc. 2. Check the saw blade for damage, whether the tooth profile is complete, whether the saw blade is smooth and clean, and whether there are other abnormalities to ensure safe use. 3. When assembling, make sure that the arrow direction of the saw blade is consistent with the direction of rotation of the device spindle. 4. When installing the saw blade, keep the shaft center, the chuck and the flange clean. The inner diameter of the flange is the same as the inner diameter of the saw blade. Make sure that the flange is tightly combined with the saw blade, install the positioning pin and tighten the nut. The size of the flange should be appropriate and the outer diameter should be no less than 1/3 of the diameter of the saw blade. 5. Before the equipment is started, ensure the safety. If there is a single person operating equipment, jog and idling, check whether the equipment is turning correctly, whether there is vibration, the saw blade is idling for a few minutes, no slip, swing or beat normally. jobs.
(3) Requirements for use:
1. When working, the workpiece should be fixed, the profile positioning should conform to the direction of the knife, so as to avoid abnormal cutting. Do not apply side pressure or curve cutting. The feed should be smooth and avoid the impact of the blade touching the workpiece, resulting in damage to the saw blade, or The workpiece flew out and an accident occurred. 2. When working, if the sound and vibration are abnormal, the cutting surface is rough, or the odor is generated, the operation must be terminated immediately, and the fault should be checked in time to eliminate the accident to avoid accidents. 3. When the pipe cutting machine starts cutting and stops cutting, do not feed the knife too fast to avoid broken teeth and damage. 4. If cutting aluminum alloy or other metal, use a special cooling lubricant to prevent the saw blade from overheating, causing paste, and other damage, which affects the cutting quality. 5. The equipment flute and slag suction device ensure smooth flow to prevent slag from forming into blocks, which affects production and safety. 6. When dry cutting, please do not cut continuously for a long time, so as not to affect the service life and cutting effect of the saw blade; wet film cutting should be cut with water to prevent leakage.
(4) Saw blade maintenance:
1. If the saw blade is not used immediately, it should be laid flat or suspended by the inner hole. The other pieces or feet should not be stacked on the flat saw blade, and the moisture should be protected against rust to avoid the cutting process. The burr, on the deburring machine, will not be able to clean the burr because the burr is too large. 2. When the saw blade is no longer sharp and the cutting surface is rough, it must be repaired in time. Grinding can not change the original angle 3. The inner diameter correction of the saw blade, the positioning hole processing, etc. must be carried out by the factory. If the processing is poor, it will affect the product use effect, and may be dangerous. In principle, the reaming should not exceed the original aperture of 20mm, so as not to affect the balance of stress. 4. The choice of alloy grinding wheel. 1) The resin bond diamond grinding wheel has weak bonding strength, so the self-sharpening property during grinding can be good, it is not easy to block, the grinding efficiency is high, the grinding force is low, the grinding temperature is low, and the disadvantage is that the wear resistance is poor and the wearer wears out. Large, not suitable for heavy duty grinding. 2) Ceramic bond diamond grinding wheel has better wear resistance and bonding ability than resin binder. It has sharp cutting, high grinding efficiency, no heat and clogging, less thermal expansion, easy control precision, and has a rough grinding surface and high cost. . 3) Metal bond diamond grinding wheel has high bonding strength, good wear resistance, low wear, long service life, low grinding cost and high load, but poor sharpness and easy blockage. 4) Abrasive grain size has a certain influence on the clogging and cutting amount of the grinding wheel. Compared with the fine sand grain, the coarse sanding grain has a larger wear depth of the cutting edge, and the grinding wheel is easy to block. 5) The hardness of the grinding wheel has a great influence on the blockage. The high hardness of the grinding wheel is high, which is not conducive to surface heat dissipation, but it is beneficial to improve the processing precision and durability. 6) Grinding wheel concentration selection is an important characteristic, which has a great influence on grinding efficiency and processing cost.
The efficiency is loud, on the contrary, the abrasive particles are easy to fall off, but the optimal binder concentration range is also optimal.